4つのグループが連携することで実際に作製可能なボディ構造の実現を目指す
「しかし残念ながら、単にトポロジー最適化システムをマルチマテリアルに適用しただけでは、理想的な構造はわかりますが、実際にその解析結果通りに作ることができるわけではありません。大きな課題はトポロジー最適化システムによって得られた最適化結果をいかにして、実設計に変換し、ボディ部品を実際に製造できるようにするかということです」と西脇教授。
そのため、西脇教授の研究開発チームでは、次のような研究・技術開発実施体制を作り、プロジェクトを進めています(図3)。
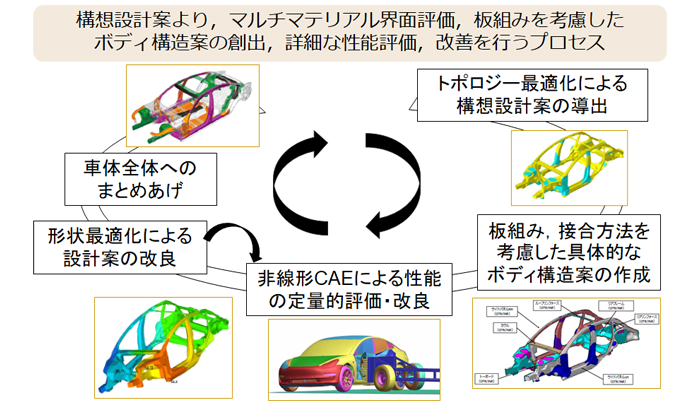
図3.マルチマテリアル実設計への適用
グループは大きく4つに分かれています。まず、「基礎技術開発グループ」では、京都大学が、マルチマテリアルに適用可能なトポロジー最適化システムの基礎技術の開発を進めています。次に、「システム構築グループ」では、CAD/CAMシステムのコンサルティング及び受託、研究・開発事業を展開しているアルモニコス社と京都大学が、開発したトポロジー最適化システムがCADのもと利用できるように、システムの構築を行っています。一方、「界面評価・モデル化グループ」では、CAE(Computer Aided Engineering:コンピュータを用いた性能評価技術)の受託解析事業を展開するメカニカルデザイン社が中心となり、マルチマテリアルの界面強度や衝突性能の数値解析モデルの構築を担当しています。そして、「適用可能性検討グループ」では、トヨタテクニカルディベロップメント社(TTDC)が、自動車技術会からの助言のもと、数値解析結果によって得られた最適構造から実設計が可能かどうかといった妥当性の検証と実ボディ構造案の作成を、また、京都大学と自動車技術会が、ボディ構造への適用可能性の検討を進めています。
「中でも我々の研究開発チームにとって大きな存在が自動車技術会です。トポロジー最適化による数値解析結果から得られたボディ構造を実設計に不可欠な板組み構造としてシステムによって自動変換することはまだ難しく、現在、直面している最も大きな課題です。しかし、自動車技術会の方々による助言を基に、今後、自動変換システムの構築を目指します。また、最終年度である2022年度中には、実用性のあるボディ部品を提案していく計画です(図4)」と西脇教授。
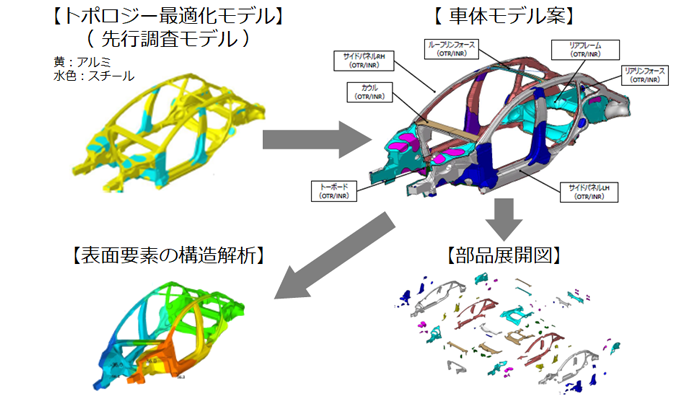
図4.マルチマテリアル実設計への適用