マルチマテリアル車体軽量化に関わる革新的設計技術の開発
本研究ではマルチマテリアル構造設計に適した解析手法であるトポロジー最適化法を適用した設計ツールを開発しています。具体的には解析対象のモデル化、解析結果の可視化とトポロジー最適化法を連携した解析システムの構築、異材接合を対象としたマルチマテリアル界面評価・モデル化の検討、車体構造適用可能性検討を行い、設計ツールとして完成させます。最終的に本プロジェクトの開発材料・接合手法による詳細設計を行い、マルチマテリアル設計車体の提案を行います。
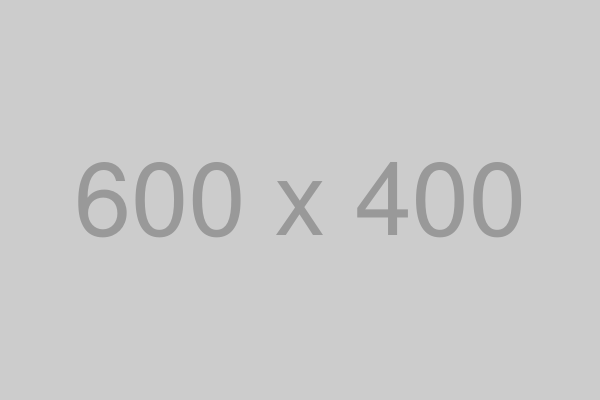
開発予定システム
研究成果
本研究ではマルチマテリアル構造設計に適した解析手法であるトポロジー最適化法を適用した設計ツールを開発しています。具体的には解析対象のモデル化、解析結果の可視化とトポロジー最適化法を連携した解析システムの構築、異材接合を対象としたマルチマテリアル界面評価・モデル化の検討、車体構造適用可能性検討を行い、設計ツールとして完成させます。最終的に本プロジェクトの開発材料・接合手法による詳細設計を行い、マルチマテリアル設計車体の提案を行います。
構造材料用接着技術の開発
マルチマテリアル構造の実現には、プロセス温度が比較的低温で、変形が少なく、剛性を確保できる接着接合が適しています。接合強度や耐久性、生産性の課題を解決するため、新規接着剤の開発や、接着メカニズム解明と評価法の確立、接合部の耐久性を向上する手法の確立を目指しています。
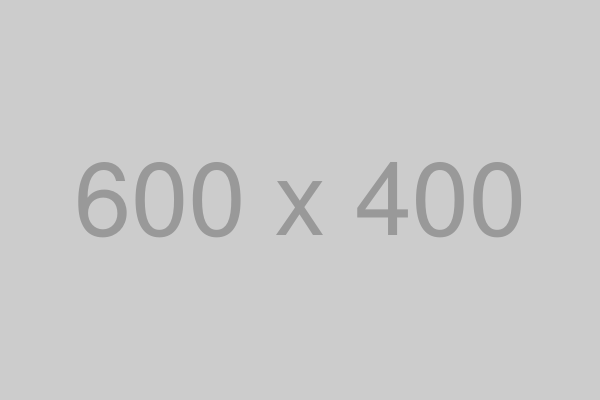
ターゲットとする性能
研究成果
両面複動式摩擦攪拌接合(フラットFSW)技術の開発
複動式ツールを用いてツールの耐久性を向上させるフラットFSW法を開発しています。またX線透過装置によってFSW中のトレーサーの軌跡を三次元で可視化することに成功しました。
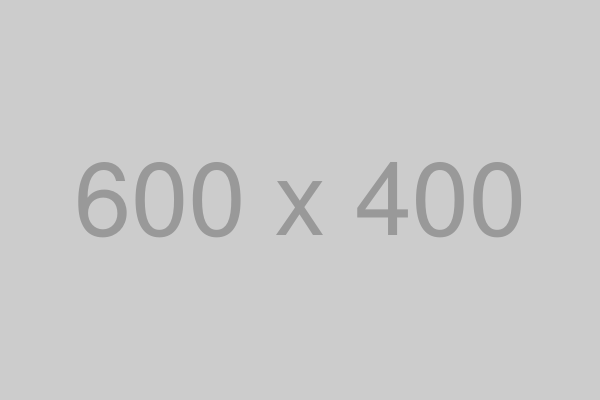
フラットFSW装置(左)とX線透過装置(右手前)
超高強度鋼の摩擦点接合(FSJ)用長寿命ツールを開発
従来材では204打点で摩耗していたツールが、開発素材では2674打点(2017年)まで耐久性が向上し、実用化に近づいています。
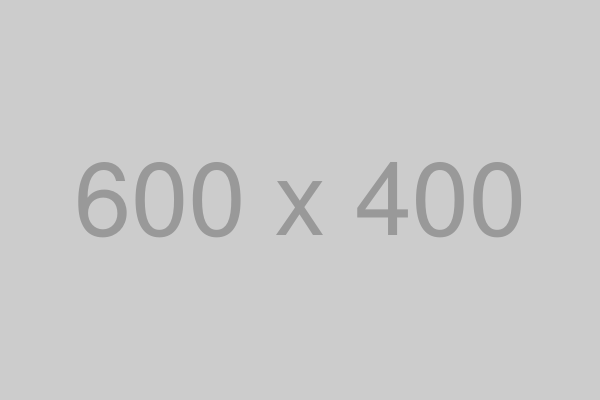
実接合による開発ツール素材の耐久性評価
革新的チタン材の開発
コストダウンを目指したチタン製造プロセスの開発を行っています。革新的な精錬プロセス技術開発と省工程による薄板製造プロセスのコスト低減を狙ったテーマでは、ラボスケ-ルでの検討を終え、スケールアップの段階に入りました。また、低廉原料利用時の溶融チタン中の脱酸プロセス技術開発(ラボスケ-ル)や強度、被削性に優れるチタン合金開発などに成功しています。加えて、従来のクロール法に替わる新精錬法「電析法」は実用化を目指して開発を進めています。
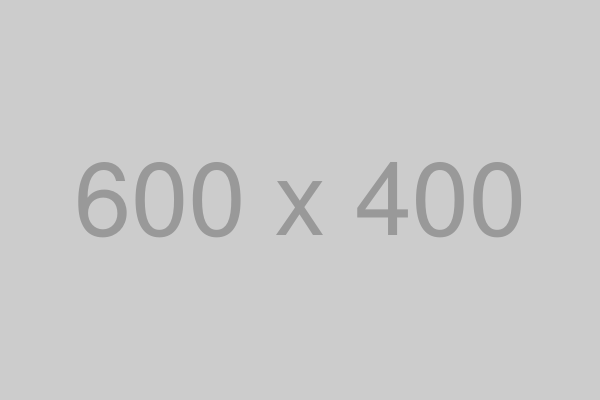
ターゲットとする性能
研究成果
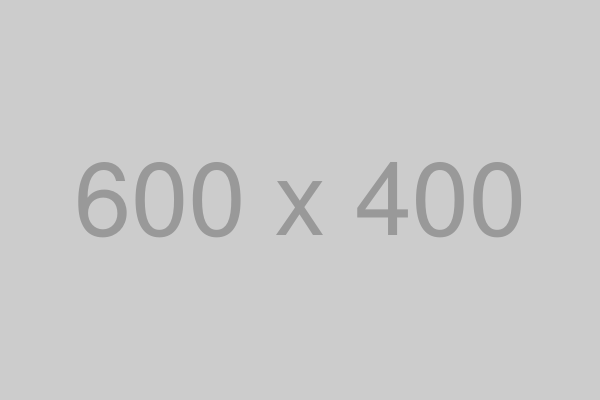
高Feスポンジチタン自動選別機
革新的マグネシウム材の開発
難燃性と加工性に優れたレアアースフリーのマグネシウム合金を開発し、現在アルミニウム材が主体の高速鉄道車両構体をマグネシウム材に置き換えることを目指しています。2018年には世界最大級となる現行の新幹線車両と同一断面サイズで1m長のモックアップ部分構体を試作しました(P2写真)。今後はさらに長尺(約5m)のモックアップ部分構体を試作し、長期使用時の安全性の検証試験を実施する予定です。また2018年度からマグネシウム材の性能・寿命を予測するためのMI(マテリアルズ・インテグレーション)活用技術の開発にも着手しています。
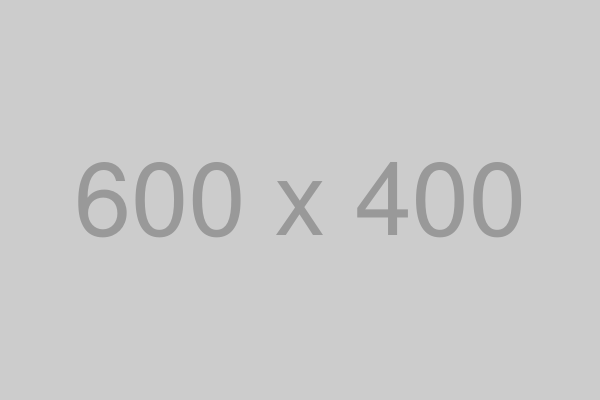
難燃性マグネシウム合金製高速鉄道車両試作構体
研究成果
開発した合金と素形材の種類
開発Mg合金 | 合金組成(質量%) | 構体適用箇所 | |
---|---|---|---|
高速押出用Mg合金 | AX41押出用合金(易加工性) | Mg-4Al-1Ca | 屋根・側面 |
高強度Mg合金 | AX92押出用合金 | Mg-9Al-2Ca | 台枠の横はり |
AX81G中板・厚板用合金 | Mg-8Al-1Ca | 床板 | |
AX81S薄板用合金 | Mg-8Al-1Ca | 室内床受 |
側パネルを試作
開発した難燃性マグネシウム合金の押出材を使用して、高速車両構体の一部を再現した側パネル(窓枠周りの構体側面)を試作。剛性の等しいアルミニウム合金製パネルより20%以上軽量化が可能なことを確認しました。
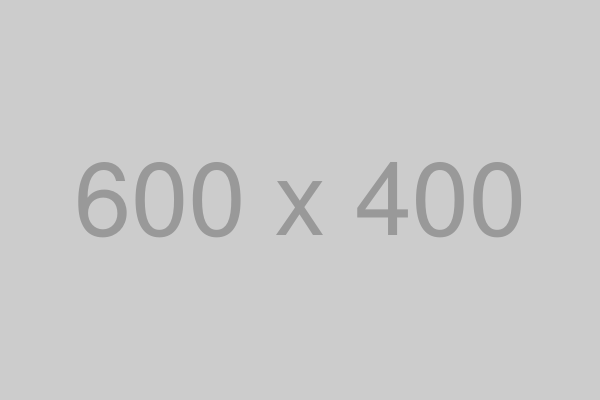
側パネル
革新的鋼板の開発
世界最高性能の自動車用超高強度鋼板を目指し、従来の590MPa級鋼板の2.5倍の引張強度1.5 GPaかつ従来の590MPa級鋼板と同等の伸び20%を有する、レアメタルを極力使用しない安価な炭素を活用した薄鋼板をラボレベルで開発することを目標とし、2017年度までに達成しました。
研究成果
材料性能の最終目標
複動式ツールを用いてツールの耐久性を向上させるフラットFSW法を開発しています。またX線透過装置によってFSW中のトレーサーの軌跡を三次元で可視化することに成功しました。
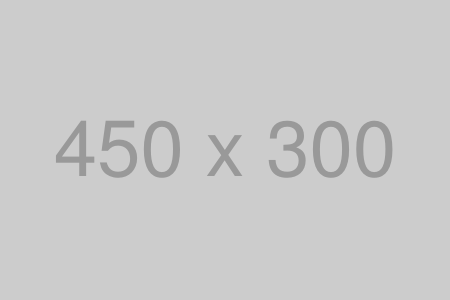
キャプションが入っていません
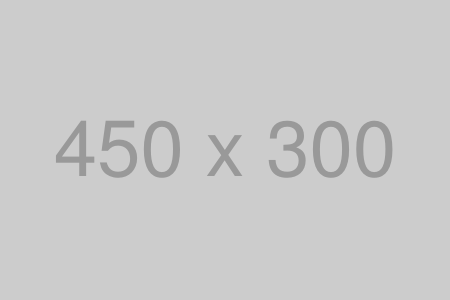
破壊挙動の解析・評価を加速する自動粒子分析装置
熱可塑性CFRPの開発
量産車に適用する熱可塑性CFRPの大型部材の高速成形技術の基盤技術を確立するとともに、多様な高強度・高機能材とのハイブリッド成形技術により、車体構造への適用拡大と実用化を目指しています。2017年には熱可塑性CFRP製シャシーを試作し、現行アルミ製より10%の軽量化に成功ました(P2写真)。さらにCFRPリサイクル技術開発により、ライフサイクルアセスメント(LCA)上優位な省エネルギー技術を開発しています。
研究成果
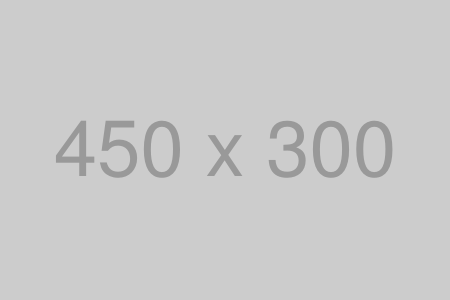
熱可塑性CFRP製試作シャシー
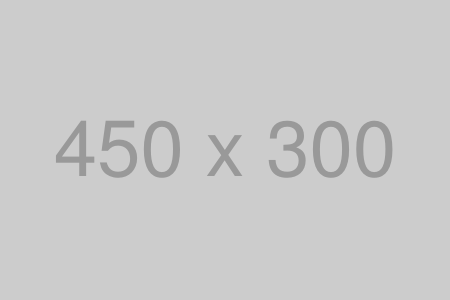
大物LFT-D高速成形設備システム
革新炭素繊維基盤技術開発
アクリル繊維を空気中高温で耐炎化・炭素化(焼成)する現行の炭素繊維製造方法を一新して、省エネルギーで生産性の高い革新炭素繊維製造プロセスの基盤技術の確立を目指しています。世界で初めて溶媒可溶性耐炎ポリマーの合成に成功し、マイクロ波による炭素化技術は、直接加熱の特徴である秒単位での高速炭素化を大繊度前駆体繊維においても実現しました。今後は炭素繊維として単糸径7μmで、弾性率240GPa、強度4GPaを凌ぐ性能を目標とし、工業化プロセス技術の完成を目指します。
研究成果
新規炭素繊維前駆体化合物の開発
世界で初めて溶媒可溶性耐炎ポリマーの合成に成功し、紡糸に関しては6Kフィラメントでの基礎技術を確立しました。炭素繊維物性は単糸径5μmで弾性率240GPa、伸度1.5%を達成しました。
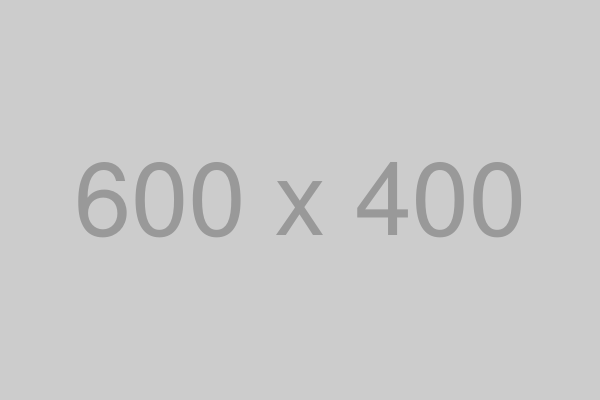
(キャプションが入っていません)
炭素化構造形成メカニズムの解明
マイクロ波による直接加熱の特徴である秒単位での高速炭素化を大繊度前駆体繊維においても実現しました。ラージトウ(48K)で安定した品質の炭素繊維が得られることを見出しています。この炭素化に伴う炭素繊維構造の形成過程と機械特性との相関解明を進めるうえで、マイクロ波の照射条件や繊維加熱メカニズムの違い、構造変化の差異を定量的に精緻に評価する新手法を開発し、安定炭素化を実現する基盤技術を開発しました。
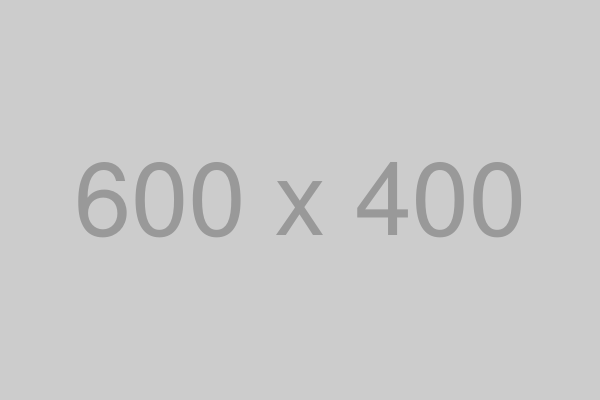
(キャプションが入っていません)